Discover the Top Advantages of Utilizing Defoamers in Industrial Processes
The usage of defoamers in commercial processes offers a series of compelling advantages that can enhance functional efficiency and item high quality. By effectively managing foam manufacturing, these agents not just optimize product flow yet also add to significant price reductions and boosted sustainability. Their application spans numerous industries, which questions regarding their role in mitigating environmental influence while guaranteeing regular output. Comprehending these benefits is vital for industries aiming to improve their processes. The ramifications of taking on defoamers may be a lot more extensive than initially viewed. What details benefits could your organization harness?
Enhanced Process Effectiveness
Maximizing commercial procedures frequently involves attending to lathering problems, which can impede functional efficiency. Foam formation can interfere with the proper functioning of equipment, reduce the effective utilization of resources, and make complex the surveillance of crucial parameters. By executing defoamers, industries can effectively mitigate these issues, bring about structured procedures and enhanced productivity.
Defoamers work by destabilizing the foam framework, permitting fast collapse and considerable reduction in foam volume. This activity not only boosts the circulation of products through equipment, such as reactors, pipelines, and mixers, however likewise minimizes interruptions brought on by foam overflow. Devices downtime is decreased, permitting for a much more effective and continual manufacturing procedure.
In addition, the use of defoamers can bring about minimized energy usage. With less foam to take care of, pumps and compressors can run a lot more efficiently, causing lower functional costs and a total improvement in procedure throughput. Ultimately, the critical use of defoamers not only addresses prompt frothing difficulties but additionally adds to a much more effective industrial community, cultivating a competitive advantage in a requiring market.
Improved Product High Quality
The assimilation of defoamers in industrial processes plays an important duty in enhancing product top quality. By effectively managing foam development, defoamers add to the consistency and uniformity of end products. Too much foam can lead to aeration, which adversely influences the texture and stability of formulas, specifically in industries such as food and coverings, pharmaceuticals, and drinks.

Furthermore, defoamers help with better blending and dispersion of ingredients, bring about homogeneity in formulas. This is important in applications where precise active ingredient ratios are critical for efficiency and security. Additionally, the removal of foam can decrease the threat of contamination during manufacturing, additional safeguarding item integrity.
Inevitably, by enhancing item high quality, defoamers not just improve customer fulfillment but additionally reinforce brand credibility. Their duty in maintaining high-grade requirements emphasizes their significance in modern-day industrial procedures.
Cost Reduction Advantages
Implementing defoamers in industrial processes can lead to considerable price reduction advantages. By successfully controlling foam formation, defoamers lessen item loss during production, therefore optimizing material use. This decrease in waste translates directly right into reduced resources costs, improving total functional efficiency.
Furthermore, making use of defoamers can decrease energy usage. Too much foam can hinder equipment performance, causing raised power needs to maintain production degrees. By minimizing foam, defoamers facilitate smoother operations, enabling machinery to run a lot more successfully and lowering websites power expenses.
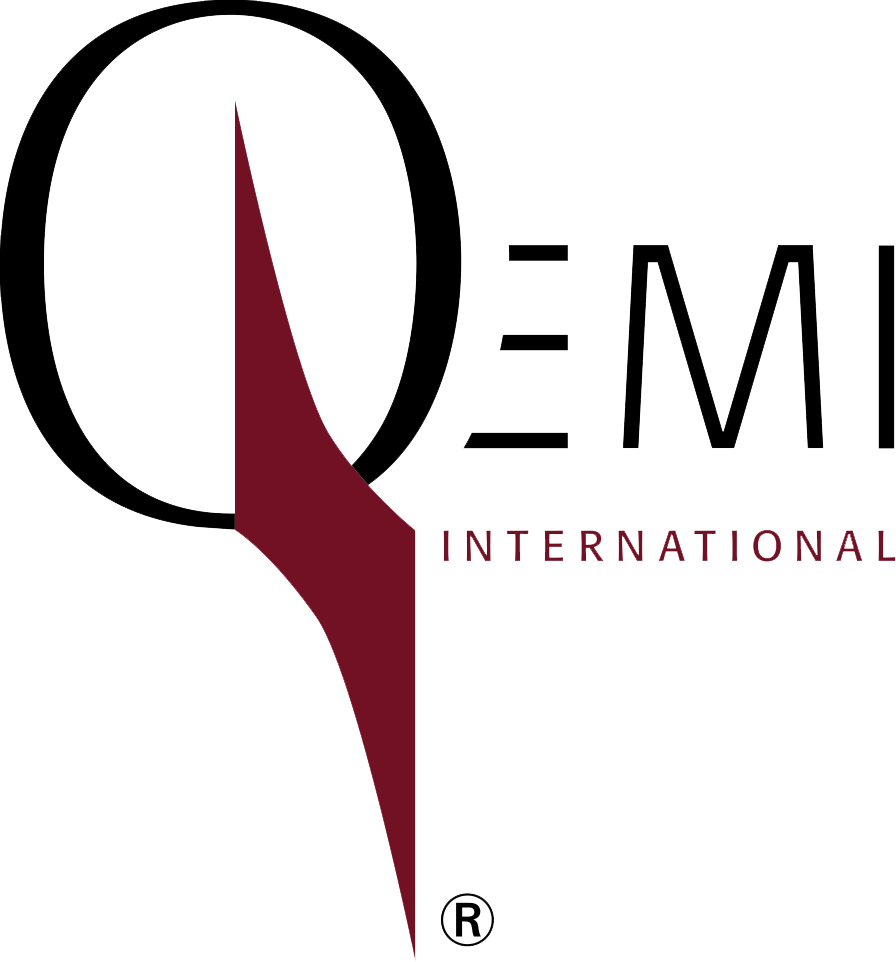
Furthermore, defoamers can shorten processing times. By making use of defoamers, sectors can enhance their processes, leading to faster turnaround times and improved throughput.
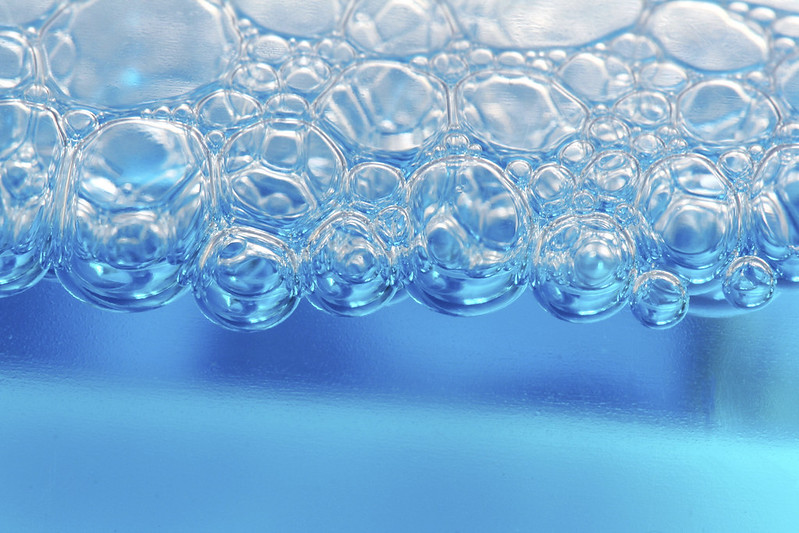
Environmental Impact Mitigation
In commercial procedures, making use of defoamers plays an important duty in mitigating ecological effects related to foam generation. Foam can lead to considerable functional inefficiencies, resulting in boosted exhausts and waste generation. By effectively controlling foam, defoamers assist preserve procedure performance, thus decreasing the total ecological impact of procedures.
Moreover, excessive foam can overflow containment systems, resulting in spills that may pollute dirt and water sources. Defoamers aid minimize this risk by ensuring that lathering does not surpass recommended limitations, advertising compliance with environmental guidelines. This aggressive strategy not only safeguards communities but also enhances the sustainability of industrial practices.
Additionally, using defoamers can lower energy consumption in various procedures. defoamers. Minimizing foam development reduces the requirement for extra energy-intensive procedures, such as boosted anxiety or pumping, which may or else be essential to take care of foam. The fostering of defoamers lines up with broader sustainability goals by advertising power effectiveness while minimizing the carbon impact of industrial activities.
Inevitably, incorporating defoamers into industrial procedures is a calculated step that supports ecological stewardship and accountable source administration.
Flexibility Throughout Industries
Across various markets, defoamers demonstrate impressive adaptability, adapting to the details requirements of diverse applications. In the food and drink industry, as an example, defoamers are critical to preserving item high quality by preventing foam development throughout processing, which can affect structure and flavor. In the pharmaceutical sector, defoamers view it now guarantee the security of formulas, boosting product effectiveness and uniformity.
In the chemical manufacturing world, defoamers facilitate smoother procedures by minimizing foam in response vessels, visit this page thus enhancing return and decreasing downtime. The paper and pulp sector counts on defoamers to improve the performance of pulp processing and paper production, guaranteeing optimal product honesty. Additionally, in wastewater therapy centers, defoamers play an important function in regulating foam during aeration processes, causing better therapy outcomes.
The flexibility of defoamers encompasses the oil and gas sector, where they assist in managing foam in boring liquids and manufacturing procedures. By customizing solutions to fulfill specific industry requirements, defoamers work as vital devices that improve functional performance, product quality, and overall process effectiveness across a wide range of industries. Their versatility highlights their value in modern-day industrial applications.
Conclusion
Finally, the application of defoamers in commercial processes presents countless benefits, including enhanced effectiveness, enhanced product top quality, considerable expense reductions, and favorable environmental impacts. Their capacity to successfully manage foam formation adds to functional continuity and resource optimization. The adaptability of defoamers across varied markets underscores their important role in advertising sustainable techniques and success. The assimilation of defoamers represents a critical approach to resolving challenges linked with foam administration in numerous producing settings.
Inevitably, the tactical usage of defoamers not just addresses prompt foaming challenges however additionally contributes to a much more reliable commercial ecosystem, promoting an affordable benefit in a requiring market.
In commercial procedures, the usage of defoamers plays an important function in mitigating ecological influences connected with foam generation. By effectively controlling foam, defoamers help maintain process effectiveness, consequently minimizing the total ecological impact of procedures.
Furthermore, in wastewater treatment facilities, defoamers play a crucial duty in regulating foam throughout oygenation processes, leading to enhanced treatment outcomes.
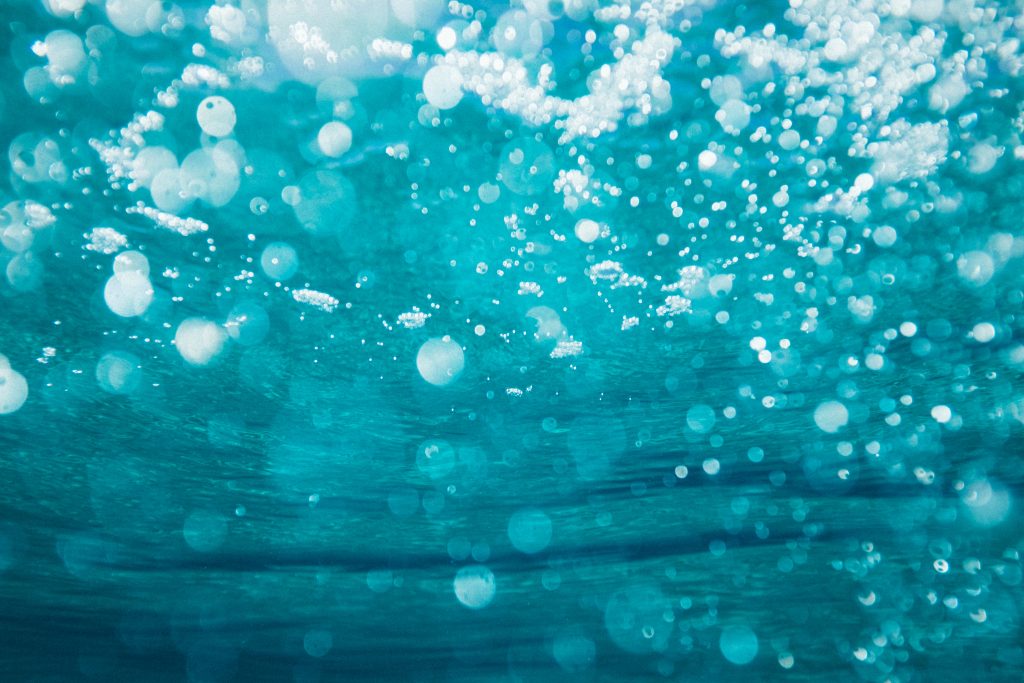
Comments on “Defoamers and Their Impact on Reducing Foam in Liquid Systems”